EPA Type 2 Introduction
- SkillCat Team
- Jan 13
- 6 min read
EPA Type 2 Chapter 1
Introduction
In this module, we will go over the EPA’s classification method for the types of systems included in Type II. We will also discuss and refresh a few basic concepts required to understand the systems. Skip to quiz!
Introduction

An EPA Section 608 Type II Certification will allow a technician to work on high or very high-pressure appliances, except small equipment and MVACs. Small appliances are covered in EPA Section 608 Type I. MVACs refer to Motor Vehicle Air Conditioning systems. A different section of the EPA covers these systems.
Defining High-Pressure Appliances
As we’ve defined, EPA Type II appliances are high-pressure appliances. A high-pressure appliance is any appliance that requires high system pressures to convert refrigerant from a gas to a liquid. Let’s review some fundamental concepts to understand this better.
Recall that during the refrigeration cycle, refrigerant moves through a piece of equipment called the condenser. The condenser converts the refrigerant from gas to liquid. This process removes heat from the refrigerant, cooling it.
When using low-pressure refrigerants in low-pressure appliances, the required pressure to convert gas to liquid is very low. However, when using high-pressure refrigerants in high-pressure appliances, the required pressure is much larger. We will learn more about low-pressure refrigerants in EPA Type III.
Common examples of high-pressure systems include residential air conditioners, residential heat pumps, supermarket refrigeration systems, rooftop units, and high-pressure chillers
A few examples of high-pressure refrigerants used in Type II systems are:
R-22
R-407A
R-407C
R-410A
R-502
Memorize this list!
Defining Regulated Refrigerants

Regulated refrigerants, as the name suggests, are regulated and have venting prohibitions imposed by the EPA. As of the EPA's latest 2019 updates, regulated refrigerants contain CFCs, HCFCs, HFCs, and HFOs.
In this topic, we reviewed the refrigeration cycle and the basics of it. We also discussed the EPA Section 608 Type II systems. We also understood the meaning of regulated refrigerants. Understanding these concepts will help us understand the different techniques and regulations laid by the EPA.
Key Secondary Components
In this module, we will learn about a few components that are not a part of the primary refrigeration cycle but play an important role for refrigeration appliances to work correctly. Skip to quiz!
Refrigeration Cycle - Secondary Components
Recall that the four critical components of a refrigeration cycle are:
Evaporator
Compressor
Condenser
Metering Device
Apart from these, the system's and other equipment's safe and smooth functioning requires a few other components in the refrigeration cycle.
Recall that refrigerant fluid flows in the refrigeration system. A storage container is required to store the refrigerant in the system, which is not in circulation. A receiver tank is that component that acts as a storage vessel.
Recall that the refrigerant comes out of the condenser through the liquid line. This refrigerant is a high-pressure liquid. The receiver tank stores this liquid. We install the receiver tank is on the liquid line as close as possible to the condenser coils' outlet.
A receiver tank is also known as a liquid line receiver tank. It is generally seen in heat pumps and residential split systems using a TXV/TEV as a metering device.
Recall that the vapor line connects the evaporator and the compressor. The refrigerant flowing out of the evaporator and into the compressor should ideally be complete vapor. But sometimes, there may be some liquid refrigerant along with the vapor.
The compressor of a refrigeration system is not manufactured to handle any liquid refrigerant. So to avoid the liquid refrigerant flowing into the compressor and damaging it, an accumulator tank is attached to the refrigeration circuit just before the compressor.
An accumulator tank is a component that protects the compressor in the system. It temporarily stores the liquid part of the refrigerant coming out of the evaporator through the suction line.
For servicing and repairing the refrigeration appliance, a component is required to allow easy access to the refrigerant flowing inside the tubes without venting it. A shut-off valve is that component. A shut-off valve is also called as the service valve.
As you can see by the arrows in the image, we can change the direction of the refrigerant fluid flowing inside the refrigerant tubes by pulling it back (back seated) or pushing it front (front seated). A gauge port is where the service hose or refrigerant gauges are connected.
To reiterate the positions of the shut-off valve, when the valve is
Back-seated: Service/gauge port is closed
Front-seated: The outlet port is closed
Neutral-seated: All ports are open
Memorize these positions!
The shut-off valve is found in both the suction and discharge lines of an appliance. The shut-off valve found on the suction side is called a suction shut-off valve. One on the discharge side is called the discharge shut-off valve.
Additional Components
A few other components are required in the refrigeration system that act as additional support for the appliance and the technician.
Recall that moisture present in the refrigeration cycle can form acidic sludge and damage the components if it reacts with the refrigerant. A filter drier is a component in the refrigeration cycle that filters out moisture and other solid contaminants from the refrigerant.
As the name suggests, moisture indicating sight glass is used to check for signs of moisture inside a refrigeration system.
It has transparent glass on it. If present in a system, moisture forms a cloudy mist on the sight glass, just like the mist formed on your car windshield on a cold day.

Recall that compressor heater are used to heat the refrigerant oil in the compressor. When the system is shut down for long periods, the pressurized refrigerant goes to the compressor, mixing with the refrigeration oil in excess quantities. The mixed refrigerant dilutes the refrigerant oil and deteriorates its quality and properties.
Heating the oil increases its temperature and boils off the refrigerant present in the oil. Heating also facilitates an easy start of the appliance and protects the components from damage due to diluted oil.
Like a user manual for any device, the nameplate provides all the data about that system. The system's nameplate is a sheet where the system's manufacturer has written down all data about that particular system.
This data includes the
Type of refrigerant
Quantity of the refrigerant
The tonnage of the system
Working pressure of the system
The voltage, current, and other electrical details.
And a lot of other information related to that system.
In this topic, we learned about the different refrigeration components and secondary components of a refrigeration appliance. Knowledge of all these components is important in understanding a refrigeration appliance.
Question #1: Which of the following refrigerants is not used in Type II systems?
R-407C
R-407A
R-245fa
R-22
Scroll down for the answer...
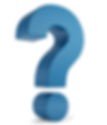
Answer: R-245fa
R-245fa is not a high-pressure refrigerant and is not used in Type II systems.
Question #2: Which of the following refrigerants would be used in a low-pressure appliance?
R-22
R-123
R-410A
R-407A
Scroll down for the answer...
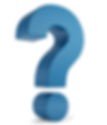
Answer: R-123
Except for R-123, all the other refrigerants are high-pressure refrigerants. R-123 is not a high-pressure refrigerant. It is a low-pressure refrigerant and not used in Type II systems.
Question #3: What is the state of the refrigerant leaving the receiver in a refrigeration system?
Low-Pressure Liquid
Low-Pressure Vapor
High-Pressure Liquid
High-Pressure Vapor
Scroll down for the answer...
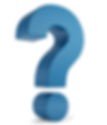
Answer: High-Pressure Liquid
The receiver tank only acts as a storage vessel for the high-pressure liquid coming out of the condenser coils. It does no other function except storage. So the refrigerant leaving the receiver is also a high-pressure liquid.
Question #4: Which of the following component is located just before the compressor?
Receiver
Accumulator
Condenser coils
TEV
Scroll down for the answer...
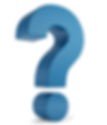
Answer: Accumulator
The accumulator tank is the component that is located just before the compressor.
Question #6: What will backseating a suction shut-off valve close?
Suction line and compressor port
Compressor and gauge port.
Compressor port
Gauge port
Scroll down for the answer...
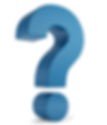
Answer: Gauge port
Back seating, a suction shutoff valve will close the gauge/service port of the valve.
Question #7: How would you remove moisture from refrigerants in a system?
Purge the condenser.
Drain the oil separator.
Reduce water flow to the condenser.
Use a filter drier.
Scroll down for the answer...
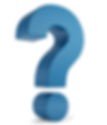
Answer: Use a filter drier
To remove moisture from refrigerants in a system, we use a filter drier.
Question #8: What is a moisture indicating sight glass useful for?
Determining the type of refrigerant.
Checking for moisture in refrigerant.
Providing sub-cooling.
Determining the type of oil used.
Scroll down for the answer...
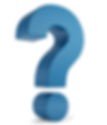
Answer: Checking for moisture in refrigerant.
Moisture indicating sight glass is used to check for signs of moisture inside a refrigeration system.
Question #9: What are refrigeration and air-conditioning compressor heaters used for?
To reduce the amount of refrigerant in the oil.
To prevent refrigerant vaporization.
To reduce the amount of entrained water in the receiver.
To prevent acid pitting
Scroll down for the answer...
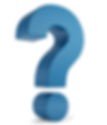
Answer: To reduce the amount of refrigerant in the oil.
The compressor heaters are used to heat the refrigerant oil and boil the refrigerant mixed with it. Heating reduces the amount of refrigerant mixed with the oil.
Question #10: What is the easiest way to check the type of refrigerant used in a 60 ton packaged rooftop unit?
Look at the unit nameplate.
Use your service gauge set and a PT chart.
Ask the owner.
Measure the condenser pressure.
Scroll down for the answer...
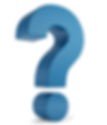
Answer: Look at the unit nameplate.
The system's nameplate is a sheet where the system's manufacturer has written down all data about that particular system. So it is the best place to look for any such information.