EPA Type 3 Introduction
- SkillCat Team
- Mar 24
- 9 min read
EPA 608 Type 3 Chapter 1
Introduction
In this module, we will learn about the meaning and different types of appliances included in EPA Type 3. We will go through the features of Type 3 appliances in this introductory module. Skip to quiz!
Definition of Type 3 Appliances
EPA Type 3 covers low-pressure appliances. Technicians working on a Type 3 appliance must be certified as either a Type 3 or a Universal technician.
Recall that the EPA Type 1 covers Small Appliances like small refrigerators and air conditioners. EPA Type 2 covers high-pressure refrigeration appliances. Commercial, industrial and large residential systems are included in it.

Type 3 appliances are classified as low-pressure appliances. This is because the pressure inside these appliances is comparatively lower than the outside atmospheric pressure. Recall that the atmospheric pressure is the pressure surrounding us.
Recall that the atmospheric pressure is 14.7 psi. The pressure inside a Type 3 appliance is anything below the atmospheric pressure of 14.7 psi. Pressure lower than the atmospheric pressure is called vacuum.
Vacuum essentially means any pressure lower than the atmospheric pressure. Type 3 appliances have a pressure lower than atmospheric pressure. So they are known to work in a vacuum. A vacuum cleaner is the best example of a device that works in a vacuum.
Recall that any matter flows from a high to low pressure. A vacuum cleaner creates a low-pressure (vacuum) that sucks all the air and dirt. Similarly, the vacuum in a Type 3 appliance wants to suck everything inside it, but it is tightly sealed.
The main example of a type 3 appliance is a chiller system. Chillers are cooling appliances that work under a vacuum. Chiller systems are mainly used to cool commercial buildings, large office spaces, and for industrial purposes.
Low-Pressure Refrigerants
The refrigeration system components in Type 3 appliances are the same as in any other refrigeration system, be it Type 1 or Type 2 systems. The major components include:

Compressor
Condenser coils
Expansion/Metering device, and
Evaporator coils
Recall that during the refrigeration cycle, refrigerant moves through the piece of equipment called the condenser. The condenser converts the refrigerant from gas to liquid. This process removes heat from the refrigerant, cooling it.
Refrigerants used in Type 3 appliances are called low-pressure refrigerants. When using low-pressure refrigerants in low-pressure appliances, the required pressure to convert gas to liquid in the appliance's condenser is very low. So the name, low-pressure refrigerants.
A few examples of low-pressure refrigerants used in Type III systems are:
R-11 (CFC)
R-123 (HCFC)
R-1233zd (HFO)
R-245fa (HFC)
Memorize this list!
Key Components
In this module, we will learn about the chillers and different components used in Type 3 appliances. Skip to quiz!
Chiller Components
Recall that chillers are cooling systems that work under a vacuum. Chillers have water flowing over the evaporator coils. So, instead of providing cool air, chillers provide cold water.
The cold water is then used to cool office spaces or used in other industrial applications. There are two main types of chillers based on the type of condenser:
Air-Cooled Chillers, and
Water-Cooled Chillers
We will learn about their working and key components in detail.
Air-cooled chillers have condensers that use surrounding air to cool hot refrigerants. The heat from the condenser is released to the air. This is similar to any residential split AC or heat pump.
Contrastingly, water-cooled chillers use water to cool the refrigerant in the condenser. The water flows over the condenser tubes and absorbs the excess heat. Cold water is used to absorb the heat from the hot refrigerant in the condenser tubes.
The cold water require to cool the condenser tubes is produced by the cooling towers. A cooling tower is a large heat exchanger unit that provides cooling water to remove heat from the refrigerants.
Recall that a chiller produces cold water by passing it through the evaporator and condenser barrels. It does so by passing copper tubes that carry water through barrels of refrigerant. The barrel carries refrigerant, and the tubes carry water for cooling.
The water-circulating pumps pump the water as they flow continuously through the tubes. The water is never allowed to mix with the refrigerant in the refrigeration cycle. Keep in mind that the water cycle and refrigeration cycle are entirely separate.
Water Box
A water box is a part of any chiller and performs the function of directing water flow. It also separates the entrance and the exit of the water into the condenser tubes. It is mounted on the evaporator and condensers of water-cooled chillers.
The water box also performs the function of sealing the chiller barrel tubes from the outside. Evaporator tubes are known as chiller barrel tubes. Keep this in mind as these names are used interchangeably.
Purge Unit
Recall that the vacuum in Type 3 appliance wants to suck everything inside it, but it is tightly sealed. All low-pressure systems have purge units to vent or remove air and moisture that enter due to leaks. The term “purge” means to remove something.
In the refrigeration appliance, the air entered into the system collects at top or highest point in the system. This is similar to how air bubbles in a bottle of water collects at the top. The collected air and moisture is then thrown out of the system by the purge unit.
In the refrigeration system, the far end of the condenser is where the air collects. As a result, this is where the technicians should make the purge unit connection.
The purge unit is located at the top of the condenser coils. The refrigerant is sucked into the purge unit from the top of the condenser. The refrigerant free from air and moisture is then sent to the evaporator through the expansion valve.
While the purge unit is operating, the refrigerant might exit the system along with air and moisture. A high-efficiency purge unit will remove minimal refrigerant along with the air. On the other hand, an inefficient purge unit will continue to leak refrigerant in large amounts.
Rupture Disc
A rupture disc is a safety disc that protects the system from getting over-pressurized. As Type 3 appliances operate at very low pressures, over-pressurization is a common mistake by many technicians. Over-pressurization causes the tubes in the appliance to burst and must be prevented at all costs.
The rupture disc is located on the evaporator of a chiller. While charging the system, we charge it through the charging valve of the evaporator. A charging valve is a port that allows a controlled flow of the refrigerant fluid in or out of the system.
The rupture disc in a chiller is set at a pressure of 15 psig. This pressure is known as safety-relief pressure. If the systems' pressure exceeds 15 psig, the rupture disc will burst, venting the refrigerant out of the system.
Recall that charging means filling the system with refrigerant. The pressure while charging through the evaporator valve should not exceed 10 psig. The difference of 5 psig (15-10) is kept while charging the system for safety purposes.
Drain Valve
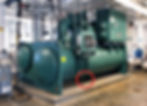
A drain valve in a chiller performs the function of allowing excess water vapor to escape into the atmosphere. The excess water vapor in a chiller finds its way into the compressor and other parts where it should not go. Releasing the moisture helps to prevent corrosion that eventually damages the compressor and shortens its lifespan.
Low Pressure Refrigerants
In this module, we will have a detailed look at Type 3 refrigerants. We will look at their characteristics and their significance. Skip to quiz!
Low-Pressure Refrigerants
Type 3 refrigerants are called low-pressure refrigerants as they are used in low-pressure appliances. Type 3 refrigerants include:

R-11 (CFC)
R-123 (HCFC)
R-1233zd (HFO)
R-245fa (HFC)
Recall that boiling temperature is the temperature at which a liquid changes its state to vapor by boiling. The temperature at which vaporization (boiling) starts to occur for a given pressure is called the saturation temperature or boiling point.
Type 3 refrigerants have a very high boiling point. Recall that the refrigerant boils in the evaporator of an appliance. This boiling temperature is of R-11 when it boils in the evaporator and passes to the compressor is 74.9 °Fahrenheit.
Type 3 refrigerants have a very high boiling point compared to Type 1 and Type 2 refrigerants. The chart shows a comparison of the boiling points of Type 1, Type 2, and Type 3 refrigerants. As you can see, Type 3 refrigerants' boiling points are much higher with a positive sign.
Pressure-Temperature Relations
P-T Charts have the relationship between the pressure and saturation temperature of any substance. For any refrigerant, we can know its saturation temperature at a given pressure and vice versa. P-T mean Pressure-Temperature Charts. Let us learn to read these charts.
Consider this P-T Chart for R-123. The units for temperature are either °Fahrenheit or °Celsius, as we can see here. To find the pressure at a temperature, we look for the temperature, then look across that row for the corresponding pressure.
The term ‘vacuum’ in the unit of pressure “inches of Hg vacuum” indicates that the pressure is below atmospheric pressure. Saturation pressure above atmospheric pressure is given in psig. Saturation pressure below atmospheric pressure is given in inches Hg or in psia.

The value 40° Fahrenheit is marked in the chart, and it corresponds to 18.1 inches Hg vacuum. It means that R-123 boils at 40°F when the pressure is 18.1 inches Hg vacuum. Notice that the red pressures are below atmospheric pressure, that is, vacuum pressures and are given in the units ‘inches of Hg.'
In the chart, the value 20 inches (around 19.5) of Hg vacuum is highlighted, and it corresponds to 35 °Fahrenheit. It means R123 will boil at 35° Fahrenheit when the pressure is 20 inches (around 19.5) of Hg vacuum.
Recall that 14.7 psia is atmospheric pressure at sea level and that 14.7 psia = 0 psig. R-123 at a pressure of 14.7 psia (Or 0 psig in the chart) will boil at approximately 82°Fahrenheit. This is the saturation temperature of R-123 at atmospheric pressure.
R-123 Refrigerant
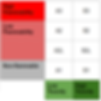
R-123 is an HCFC (Hydrochlorofluorocarbon). It contains chlorine, so it contributes to ozone depletion. Recall that chlorine-containing refrigerants deplete the ozone layer.
Recall the ASHRAE safety rating of refrigerants that rates refrigerants based on its toxicity and flammability. R-123 is rated as a B1 refrigerant in the ASHRAE safety category because it has high toxicity.
R-1233zd Refrigerant
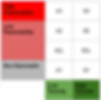
R-1233zd can be used in place of R-123. R-1233zd is neither a flammable nor a toxic refrigerant. As a result, it carries an A1 ASHRAE safety rating.
Due to its A1 rating, SNAP has approved R-1233zd as a replacement refrigerant for low-pressure systems. Recall that SNAP stands for Significant New Alternatives Policy. It is the EPA’s program to reduce the number and amount of ozone-depleting substances.
R-1233zd is an HFO refrigerant that does not contain chlorine. R-1233zd is used for large-scale applications as it is a safe refrigerant compared to other Type 3 refrigerants. Also, it has a higher efficiency than other Type 3 refrigerants.
Question #1: Which of the following refrigerants would be used in a low-pressure appliance?
R-22
R-123
R-410A
R-407A
Scroll down for the answer...

Answer: R-123
Except for R-123, all the other refrigerants are high-pressure refrigerants. R-123 is not a high-pressure refrigerant. It is a low-pressure refrigerant and not used in Type II systems.
Question #2: After the refrigerant leaves the purge unit, where does it go?
Condenser
Recovery Cylinder
Evaporator
Compressor
Scroll down for the answer...
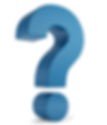
Answer: Evaporator
The refrigerant from the purge unit free from air and moisture enters the evaporator through the expansion valve.
Question #3: Which of the following components are only found in Type 3 appliances?
Compressor
Purge Unit
Condenser
Evaporator
Scroll down for the answer...
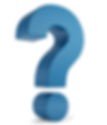
Answer: Purge Unit
Purge unit removes non-condensables that enter the low-pressure system when there is a leak in it.
Question #4: What is the safety-relief pressure of the rupture disc?
10 psig
15 psig
5 psig
20 psig
Scroll down for the answer...
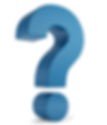
Answer: 15 psig
The rupture disc is set to burst at 15 psig. This pressure is also known as the safety-relief pressure.
Question #5: Which of the following is not a Type 3 refrigerant?
R-11
R-22
R-123
R-1233zd
Scroll down for the answer...
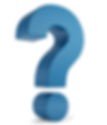
Answer: R-22
R-22 is a Type 2 high-pressure refrigerant.
Question #6: What is the boiling point of R-123?
74.9 ℉
82 ℉
-41.3 ℉
-55.4 ℉
Scroll down for the answer...
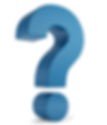
Answer: 82 ℉
The boiling point of R-123 is 82 ℉.
Question #7: What is the pressure of R-123 when it boils at 82° Fahrenheit?
20 inches of Hg
18.1 inches Hg
20.6 psig
14.7 psia
Scroll down for the answer...
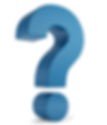
Answer: 14.7 psia
R-123 at a pressure of 14.7 psia will boil at approximately 82° Fahrenheit.
Question #8: Under what code group of Standard 34 does R-123 fall?
B1
B2
A1
A2
Scroll down for the answer...
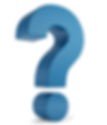
Answer: B1
The ASHRAE safety rating for flammability and toxicity of R-123 is B1.
Question #9: What is the ASHRAE safety rating of R-1233zd?
B1
B2
A1
A2
Scroll down for the answer...
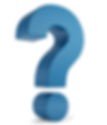
Answer: A1
The ASHRAE safety rating for flammability and toxicity of R-1233zd is A1.
Other References: