Equipment Malfunction
- SkillCat Team
- 3 days ago
- 3 min read
EPA 608 Core Chapter 31(Take full course)
In this module, we will discuss what procedures to follow when the equipment malfunctions.
1. Compressor Burnout
In the event of a compressor burnout, we need to access the damage and clean up. A compressor can burn out from high temperatures that causes its components to fail.
If a compressor burns out, the oil turns highly acidic and there will be an acidic smell. The burnout can be severe or mild, and the technician needs to access.
If you suspect a burnout or any major equipment failure, you need to take an oil sample. An oil sample will give you more details on what is wrong with the system.
To clean up a system burnout, it is important to do the following:

Install a liquid line filter-drier
Install a suction line filter-drier
Flush system with dry nitrogen
After a compressor burnout, we need to flush the system with nitrogen to get rid of oil residue in the purge lines. Alternatively, we could also use a commercial system flushing solution. Both of these are approved methods of cleaning up.
We cannot flush with liquid refrigerant to clean the field tubing. This would vent the refrigerant, and recall that this is illegal under Section 608.
Faulty components must also be replaced so that the system can function again.
2. Crankcase Migration
The compressor’s crankcase acts like a container that collects refrigerant oil in the refrigeration system.
When the system is not running, the refrigerant does not have any force or pressure acting on it. Because of this, it will naturally flow to where there is least pressure.
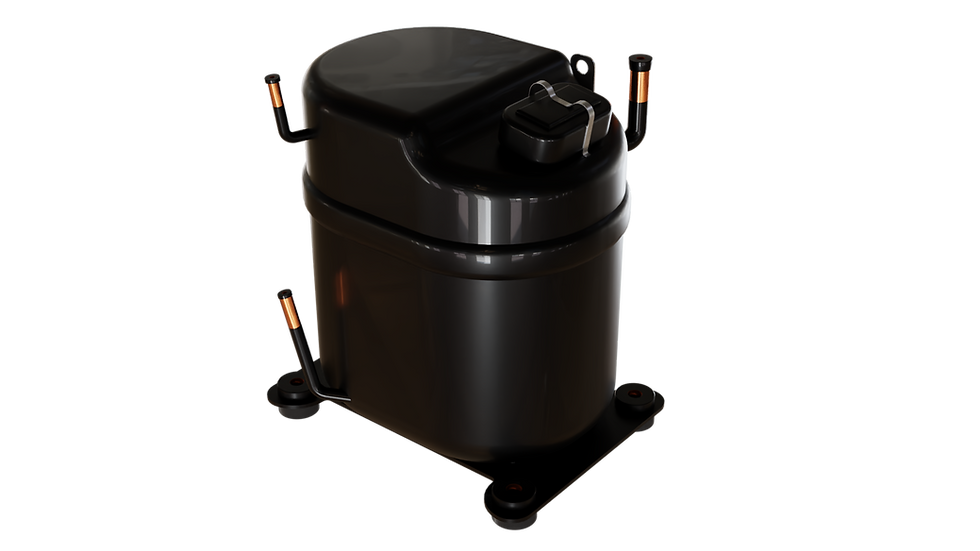
Imagine juggling some oranges. As you are juggling, the oranges are moving in a circle in the air because your hands are moving them in a circular motion. If your hands stop moving, the oranges will fall to the floor. That is the natural force of gravity acting on them.
In the same way, if the refrigeration system is not running, refrigerant will flow to the place of least pressure. The place of lowest pressure happens to be at the crankcase.
The oil pressure in the crankcase is lower than the refrigerant pressure. This is why refrigerant will migrate to the crankcase. This is also similar to how heat will travel from high to low, as we discussed in the Refrigeration Cycle.
To reiterate, the refrigerant will migrate to the crankcase in the compressor because that is the place with the lowest pressure in the system.
3. Relief Valves
In order to make sure that the system is completely safe to use, we need to replace any components that show danger of failing. This way, we prevent major failures that can create life threatening situations. Safety is always first.
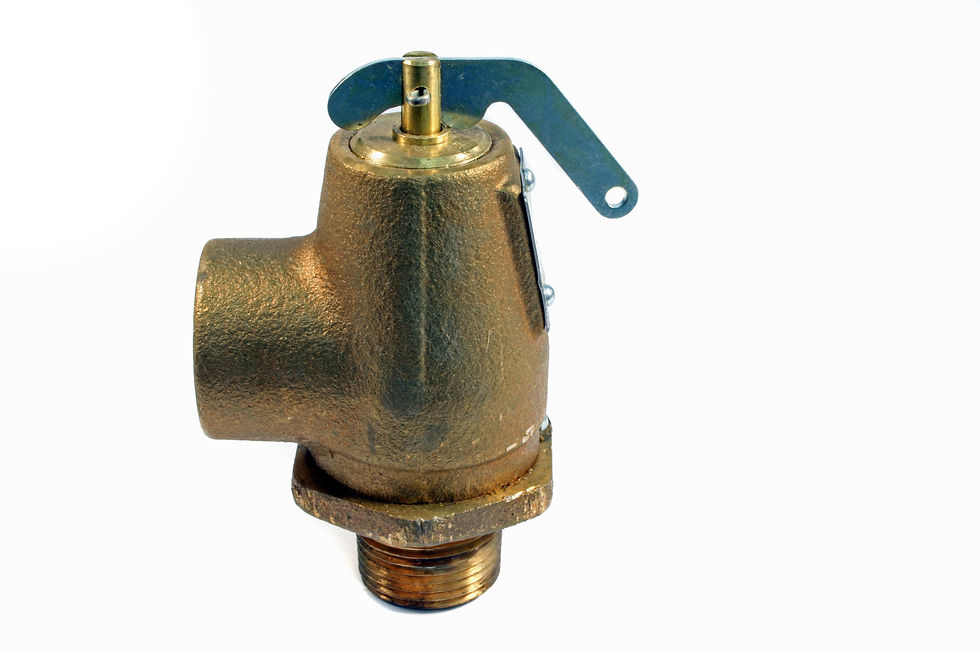
Relief valves are installed to provide insurance in case pressure builds up in the system. If is too high because of irregularities in the system, this can cause major explosions. This is a major safety concern.
If the body of relief valves show any sign of corrosion, the relief valve must be replaced. Corrosion on the body indicates damage that may prevent the relief valve from doing its job to regulate pressure.

4. Metal Components
Recall that refrigerant pipes are made of metals like steel and copper.
We have to be mindful of how refrigerants can interact with copper especially, because copper components can be oxidized by refrigerants.
5. Conclusion
In this module, we learned about the malfunctioning of equipment and discussed different ways to avoid it.
Other References: