Leak Detection in Low Pressure HVAC Equipment
- SkillCat Team
- Apr 8
- 7 min read
EPA 608 Type 3 Chapter 2
Leaks in Low-Pressure System
In this module, we will learn about leaks in low-pressure systems. We will see the different indicators of a leak and the common areas that can leak in a Type 3 system. Skip to quiz!
Leaks
Recall that any matter flows from a high to low pressure. If you come across a leaking water pipe, you can see the water coming out of it from an opening. But, this is not the case with low-pressure appliances.
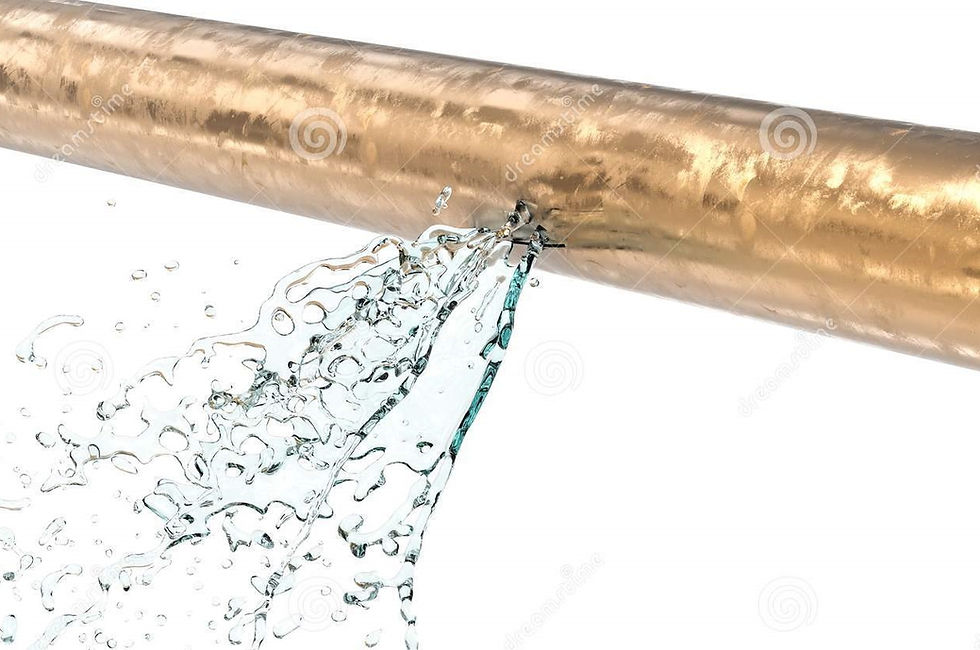
Recall that a low-pressure system operates below atmospheric pressure under a vacuum. The vacuum in Type 3 appliances wants to suck everything inside it like a vacuum cleaner. This is why Type 3 appliances need to be sealed tight to avoid the sucking of outside moisture into the system.
Recall that there is water flowing in the chiller systems’ evaporator and condenser. This water leaks into the refrigeration system to mix with the refrigerant. Apart from this leak, the outside air that contains non-condensables can also leak into the system.
Moisture is an impurity and is known as non-condensable in the system. Recall that air, moisture, and nitrogen are considered non-condensable gases in any system. Any problem in sealing low-pressure systems causes the outside air and moisture to leak inside the system.
Leak Indicators
Head pressure is also called high side pressure or discharge pressure. Recall that the discharge side of a system consists of liquid refrigerant. We can confirm the presence of non-condensable gases if the discharge side pressure in the refrigeration system is higher than normal.
The reason for a higher discharge pressure is;
The gases remain in the vapor phase and do not convert to liquid.
This exerts pressure on the refrigerant liquid, increasing its pressure on the discharge side of the appliance.
Recall that the purge unit performs the purge unit's function is to remove the moisture collected in the refrigeration cycle. Excessive moisture collection in the purge unit or excessive running of a purge unit could act as an indicator that the system is leaking.
Excessive moisture collection in the purge unit could indicate that the condenser or the chiller barrel tubes are leaking and drawing water into the system. Recall that there is water flowing in the chiller barrel and condenser. Water tubes in the chiller that suffer from leaks may need extensive repairs.
Common Leak Areas
In a belt-driven non-hermetic system, the compressor motor and the compressor are in different structures and connected by a rubber belt. Unlike the hermetic type, it does not have its components in a single shell. This type of system can be seen mostly in industrial refrigeration systems.
A Rotating shaft seal is used at the junction where the metallic shaft connects to the compressor. Rotating shaft seals have rubber seals for the purpose of sealing. If a system is non-working for several months, the rubber seals become hard and cannot perform sealing, causing leaks in the system.
To reiterate the whole concept:
A Rotating shaft seal is used at the junction where the metallic shaft connects to the compressor.
In a belt-driven non-hermetic system, that has not been used for many months, the rotating shaft seal is most likely to leak.
Fittings generally mean any part of the piping that is joined to the refrigerant tubing. All nuts, joints, bends, elbow joints, etc., pieces of refrigerant pipings are called fittings. Leaks can be due to improper assembly of the fittings or timely damage to the fittings.
A gasket is a ring of rubber or other material. Common examples of gaskets are those seen in pressure cookers. Gaskets seal the joint between two surfaces in any appliance and can leak if they are worn out.
A water box is generally fixed to the chiller barrel, and gaskets are used to seal them perfectly. Also, the compressor parts use gaskets to provide sealing. Gaskets and fittings are common components that can cause a leak.
Leak Detection
In this module, we will learn about the methods to detect leaks in low-pressure systems. Skip to quiz!
Leak Detection Methods
Vacuum testing is the process of using a vacuum pump to create a vacuum inside the system and test for leaks. Recall that a vacuum pump is the same equipment used during evacuation of a system. We will discuss evacuation in the upcoming topics.
Generally we vacuum a chiller system to 1 mm of Hg. This vacuum is held for a few minutes to see if the vacuum pressure rises. ASHRAE Guidelines 3 states that if the pressure in the system rises from 1 mm Hg to a level above 2.5 mm Hg during vacuum testing, the system should be further leak checked.
A hydrostatic test is a method used to detect leaks in oil pipelines, gas cylinders, boilers, chillers and fuel tanks. In the process of the hydrostatic test, the tube of the chiller is filled with coloured water. The water is pressurized above the operating pressure of the equipment.
The pressurized colored liquid is held there for a set time. Any leaks in the system will cause the water to ooze out of the leaking gaps or holes. The colored dye leaves a mark and helps in detecting the location of the leaks visually.
To summarize the process,
Colored water is pumped into the chiller tubes.
The water is held for some time.
Leaks are detected by searching for colored watermarks outside the tubes.
A leak detector probe is a device used to sense the presence of refrigerant outside the system. It is placed near the opening of the drain valve of the water box of the chiller to check for refrigerant gas leaks. If the refrigerant has leaked into the water system, it can be detected at the drain valve.
Once the water in the system is drained, there should be nothing coming out of the drain valve. If there is a leak, the leaked refrigerant will somehow find its way to the drain valve This can be detected by holding the leak detector probe near the valve.
In this test, the pressure of the chiller is increased while it is working to detect any leaks in the system. To increase the system pressure in a controlled way, we use hot water or electric heating blankets. Recall that as the temperature increases, the pressure increases too.
Electric heating blankets produce warmth by passing electricity through it. The gradual increase in temperature avoid temperature shock to the evaporator. Hot water is circulated throughout the system in a controlled manner to increase the pressure of the system.
The hot water also increases the pressure in the system. The increased pressure causes the liquid to ooze out of the leaking areas if present and they can be detected. The rupture disc on the evaporator may open if the pressures are raised too high so this process must be done in a controlled manner.
An electronic leak detector can then be used to detect any refrigerant leaks outside the system.
Recall that in a nitrogen pressure test, also known as standing pressure test, nitrogen gas is filled in the system to check for leaks. There is a drawback of using dry nitrogen to increase the pressure of the system for leak detection. Recall that nitrogen gas cylinders are highly pressurized.
While leak testing a low-pressure chiller with nitrogen, the maximum pressure should not exceed 10 psig. If it exceeds 10 psig, the rupture disc will burst open. So the nitrogen pressure test has to be done in a very controlled manner that requires highly trained technicians.
Question #1: Continuous excessive moisture collection in which component of a low-pressure refrigeration system could indicate a leak?
Water Box
Purge Unit
Drain Valve Outlet
Pressure Relief Valve
Scroll down for the answer...

Answer: Purge Unit
Excessive moisture collection in the purge unit could indicate that the condenser or the chiller barrel tubes are leaking and drawing water into the system.
Question #2: Which part of a belt-driven non-hermetic compressor is most likely to leak if the compressor has not been used for several months?
Suction service valve
Rotating shaft seal
One or both of the king valves
Head gasket on discharge side
Scroll down for the answer...

Answer: Rotating shaft seal
If a belt-driven non-hermetic compressor has not been used for several months, rubber seals in the rotating shaft seals become hard. A hard seal cannot perform its function of sealing the system. Insufficient sealing will let the refrigerant oil leak out of the system.
Question #3: On low-pressure chillers, water is most like to leak into the refrigerant system through;
air leaks in the rupture disc assembly.
tube leaks in the evaporator.
leaks from areas with gaskets or fittings.
leaks from the charging service valve.
Scroll down for the answer...

Answer: leaks from areas with gaskets or fittings.
Gaskets and fittings are common components that can cause a leak.
Question #4: According to ASHRAE Guideline 3, the system should be checked for leaks if during a standard vacuum test the pressure in a system rises from 1 mm Hg to a level above;
1.5 mm Hg.
2.0 mm Hg.
2.5 mm Hg.
3.0 mm Hg.
Scroll down for the answer...

Answer: 2.5 mm Hg.
ASHRAE Guidelines 3 states that if the pressure in the system rises from 1 mm Hg to a level above 2.5 mm Hg during vacuum testing, the system should be further leak checked.
Question #5: A hydrostatic tube test kit will;
determine if a tube leaks.
blow all water out of tubes.
remove water from a machine.
vent refrigerant to the atmosphere.
Scroll down for the answer...

Answer: determine if a tube leaks.
A hydrostatic test is a method used to detect leaks in chiller tubes.
Question #6: A leak detector probe to check gas leaks into the water box with water removed should be placed;
At the rupture disc seal.
Around the vent valve.
Around a test plug
In the drain valve opening.
Scroll down for the answer...

Answer: In the drain valve opening.
If there is a leak, the leaked refrigerant will somehow find its way to the drain valve. This can be detected by holding the leak detector probe near the valve.
Question #7: Leak testing a low-pressure refrigeration system with nitrogen in excess of ____ psig could cause the ____ to fail.
30; Condenser tubes
30; Purge unit shells
10; Rupture disc
20; Evaporator tubes
Scroll down for the answer...

Answer: 10; Rupture disc
While leak testing a low-pressure chiller with nitrogen, the maximum pressure should not exceed 10 psig. If it exceeds 10 psig, the rupture disc will burst open.
Other References: