EPA Type 3 Chapter 4
Recovery
In this module, we will discuss the different refrigerant recovery methods and a couple of techniques for faster recovery. We will also discuss the pieces of equipment used for the recovery process. Skip to quiz!
Recovery Equipment
A recovery machine contains a compressor to suck out the refrigerant during recovery. Water-Cooled Recovery Units are most common while recovering refrigerant from a chiller system. The advantages of these units are:
Faster Recovery.
A large amount of refrigerant can be recovered easily and quickly.
A water-cooled recovery unit uses a condenser coil that cools down the recovered vapor refrigerant and converts it into a liquid. The recovery unit’s condenser coil is similar to the condenser coil in a refrigeration appliance.

Local municipal water supply is continuously passed over the condenser coils to cool it. Other recovery machine types heat up after some time due to the large amount of refrigerants. A water-cooled recovery unit is generally used to recover large amounts of refrigerant in comparatively less time.
Recall that any low-pressure chillers have a ruptured disc. The rupture disc might burst if the pressure exceeds 10 psig at any time in the recovery process. All recovery units used for recovering from a low-pressure chiller have high-pressure cut-out control that does not allow the pressure to rise above 10 psig.
Recovery Procedure
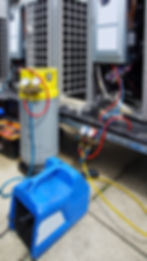
During refrigerant recovery, if there are confirmed leaks in the system, the water from the condenser and evaporator barrels must be drained from the drain valve. Recall that the pressure in the chiller barrel is decreasing continuously during the recovery process. The low pressure created by the recovery machine can suck the water from the chiller tubes via the leak openings or holes. Recall that water is an impurity when mixed with refrigerant. If there are no leaks in the system and the recovery is made for other purposes, the water in the chiller tubes need not be drained out. In such conditions, the water in the evaporator and condenser tubes must be circulated throughout the process. Recall that the water-circulating pumps always circulate water. Recall that a reduction in pressure due to recovery will also reduce the temperature in the chiller system. The water is circulated continuously during the recovery process so that it does not freeze inside the tubes. If the water is in circulation, there is no freezing chance, and ice formation is prevented. The water in the chiller tubes is never allowed to stay stationary and is either circulated or drained out. Ice formation is very dangerous as it can burst the copper pipes and damage the water circulation pumps.
Recovery Methods
The refrigerant can be recovered in liquid form or vapor form. It is necessary to recover both liquids as well as vapor refrigerant from the system for complete recovery. Let us discuss this a bit more.
While recovering, liquid refrigerant is recovered from the liquid line in the system.
Refrigerant is first recovered in liquid form for faster recovery.
As refrigerant oil is mixed with refrigerant, liquid recovery causes loss of refrigerant oil.

After liquid recovery, the remaining refrigerant is recovered in vapor form. Vapor recovery is slow & consumes more time. So to save time, the recovery process is started by removing the liquid part first.
While recovering, vapor refrigerant is retrieved from the vapor line in the system.
A lower amount of refrigerant oil is mixed with the vapor as compared to liquid refrigerant.
So vapor recovery minimizes the loss of refrigerant oil from the system during recovery.
An average 350 ton R123 chiller at 0 psig still contains 100 pounds of vapor after all the liquid refrigerant has been removed. So it is important to recover the vapor refrigerant after liquid recovery. Tonnage is the cooling capacity of any appliance. For example, we commonly say a 5 ton AC referring to its cooling capacity. Recall that atmospheric pressure is the pressure of the surroundings. Sometimes, leaks in the appliance cause air to leak inside during recovery, and a complete recovery cannot be made. In such cases, recovery from the appliance is only possible till atmospheric pressure. Note that depending on the question, the EPA exam may use the word Evacuation in place of Dehydration or in other questions in place of Recovery.
Recovery Time
Recovery time is the time it takes to recover a refrigerant. Generally, we want to recover refrigerants in the least possible amount of time.

Recall the factors affecting the time it takes to recover refrigerant:
Ambient Temperature, and
Hose Length
A higher ambient or room temperature leads to a faster recovery. The shorter the length of the recovery hoses, the faster the refrigerant flows through it.
As already discussed, liquid recovery is faster and reduces the recovery time. Recall that the pressure inside the liquid side is higher. The higher pressure pushes the liquid out of the system into the recovery tank more quickly.
In this module, we discussed the different refrigerant recovery methods. We walked through the pieces of equipment used for the recovery process. We also learned a couple of techniques for faster recovery.
Question #1: What is a typical advantage of a water cooled recovery unit?
Higher pressure at the recovery compressor's discharge.
Higher pressure in the recovery tank.
Faster recovery of large quantities of refrigerant.
A greater percentage of refrigerant recovered.
Scroll down for the answer...
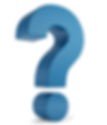
Answer: Faster recovery of large quantities of refrigerant. A water-cooled recovery unit is generally used to recover large amounts of refrigerant in comparatively less time. Question #2: A typical setting for the high pressure cut-out control on a recovery unit used for evacuating the refrigerant from a low-pressure chiller is;
2 psig.
5 psig.
10 psig.
15 psig.
Scroll down for the answer...
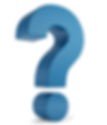
Answer: 10 psig. The rupture disc might burst if the pressure exceeds 10 psig at any time in the recovery process. All recovery units used for recovering from a low-pressure chiller have high-pressure cut-out control that does not allow the pressure to rise above 10 psig. Question #3: What should be on and what should be off during vapor removal from a low-pressure refrigeration system?
Commercial refrigeration
Industrial process refrigeration
Comfort cooling
Ice making refrigeration
Scroll down for the answer...
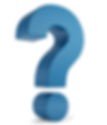
Answer: Commercial refrigeration EPA classifies appliances used in retail food and cold storage warehouse sectors as Commercial Refrigeration System. Question #4: What precaution should be taken prior to recovering refrigerant from a chiller suspected of having tube leaks?
Drain the watersides of the evaporator and condenser.
Run the circulating pumps.
Be certain the purge unit is operating.
Open the condenser vents.
Scroll down for the answer...
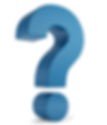
Answer: Drain the watersides of the evaporator and condenser. During refrigerant recovery, if there are confirmed leaks in the system, the water from the condenser and evaporator barrels must be drained from the drain valve. Question #5: Why must water be circulated through a chiller during refrigerant evacuation?
To speed up the recovery process.
To prevent loss of refrigerant to the atmosphere.
To prevent freezing of water in the appliance.
To maintain constant refrigerant pressure in the appliance
Scroll down for the answer...
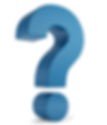
Answer: To prevent freezing of water in the appliance. Recall that a reduction in pressure due to recovery will also reduce the temperature in the chiller system. The water is circulated continuously during the recovery process so that it does not freeze inside the tubes. If the water is in circulation, there is no freezing chance, and ice formation is prevented. Question #6: Refrigerant removal from a low-pressure system starts with;
vapor removal.
liquid removal.
vapor and liquid removal.
oil separation.
Scroll down for the answer...
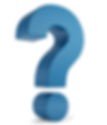
Answer: liquid removal. While recovering, liquid refrigerant is recovered before the vapor refrigerant in the system. This saves a lot of time during recovery.
Other References: